Recommendations on which brick is better to use in the manufacture of precast tape or from small-format materials are given in SP 15.13330 of 2012. Masonry is allowed from ordinary red, facing solid ceramic bricks with a width of 51 cm or more concrete blocks measuring 20 x 20 x 40 cm.With an unlimited budget, you can choose a clinker stone with the highest possible moisture resistance. For the basement part of the foundation, the requirements are much lower than for underground structures.
This is a guide only and the material you are using may vary in weight. This amount can vary from 5 to 3 liters, depending on the material that will be used in the manufacture of the block. Seal blocks may require less compressive and tensile strength than blocks that hold structures or corners. For hard blocks use ours.
Preliminary remarks on the environmental benefits of modern stabilized land in low-cost urban housing. Mainey also stated that stabilized compressed earth blocks are more environmentally friendly than refractory bricks and use less energy and pollute less refractory bricks to produce.
Despite the variety of wall materials used for masonry, only red ceramic bricks and wall concrete blocks can be used in foundations. Foundation ceramics are classified according to the following criteria:
- dimensions - normal format (NF) 6.5 x 12 x 25 cm, double (2.1 NF) 14 x 12 x 25 cm, one and a half (1.4 NF) 88 x 12 x 25 cm;
- appointment - front, private;
- frost resistance - F25, F35, F50.
Emissions of pollutants from energy consumption
9 times smaller than a brick cut with wire 4 times smaller than a brick cut with wire. 1 times less than rural refractory bricks 9 times less than rural refractory bricks. The table presents comparative analysis energy consumption and carbon dioxide emissions from four types of building materials.
Cement cement products claim that their treated roads can be opened up for immediate use; however, cement requires chemical reaction hardening to achieve maximum stability. This gives the site developer excellent quality and control tests. Water intrusion is one of the main causes of road destruction worldwide, but it has now been virtually eliminated. If required in the future, an asphalt wear surface can be added to these roads. Note. The above comparison refers to stabilizing polymers that require the addition of cement.
Moreover, manufacturers guarantee the specified values of frost resistance only for the basement part of the foundation masonry. Structures used underground have a minimum resource (one and a half times less than reinforced concrete). It is forbidden to operate brick strip foundations at a high (less than 1 m from the bottom) groundwater level (GWL) or the possibility of its seasonal rise.
South Sudan: A New Way Forward
The brick building project was launched to provide civilians with an alternative source of livestock stealing. Yak. "Each bag of cement produces 75 bricks, and the group can use five to seven bags of cement a day."
The project has also been used by women in the city, especially those displaced by conflicts in their neighborhoods. Nyachuot Chuol Kuon, 43, also joins gravel to buy food for his two children. "I am trying to survive because there was no rain last year, but there was uncertainty."
Corpulent ceramic brick- the most optimal choice.
The characteristics of a solid concrete block are different. The strength of concrete is twice as high, frost resistance is F15 - F50, the format is much larger. Each block replaces 8 bricks, the laying is done faster. The dimensions allow you to carry out masonry with a width of 40 or 60 cm without pinning.In the first case, you can save the construction budget. The second option is more often used for deep belts, in which the walls of the underground floor experience severe lateral loads.
This will enable young people to support their families by working in the trade. The Yungali state resorted to building cement blocks to support families rather than stealing livestock from their neighbors. A great way to build a safe and peaceful country. The Hoffman kiln consists of two galleries with a semicircular vault shape, 70 meters long and 3.5 meters wide, carefully insulated with walls and insulation, communicated to each other at the beginning and at the end of each gallery by what we call fires. It is built of bricks and mud.
The hot air from the cooling will dry out the brick dryer and reduce energy consumption. Our commitment is rational use energy resources and valorization of plant materials. The combustion process is very simple and consists of pulverizing the biomass to make it very thin and injecting it into the furnace through the top through solid fuel burners, with the advantage that there are practically ashes that are reused by incorporating them into the clay during the kneading process.
Attention! There are bricks measuring 6.5 x 8.5 x 25 cm (0.7 NF), made in Europe, single modules (1.3 NF) 6.5 x 13.8 x 28.8 cm, "three-quarters" 18 cm , "Halves" 12 cm, "quarters" 6 cm.
For underground structures
The main criteria when deciding which brick is better to use for underground masonry are:
The usual tones of our own and exclusive clays for our products are straw white, white and red, or salmon and reddish. Masons traditionally build brick walls with mortar. While mortar does bond bricks together, the substance can be too complex for decorative applications or sculpture projects that use bricks. Depending on your needs, you can choose from several commercial adhesive products to join bricks together or insert items into bricks.
Mortar is a light mixture of water, sand, lime and cement that is used to permanently bond bricks together to create a solid foundation. When the mortar is dry, it is similar to brick in strength and structure and can withstand precipitation. sunlight, high temperatures and high temperatures, including chimneys.
- strength - standardized only for grades M100 - M300 (2.2 - 4.4 MPa, respectively);
- water absorption - 6 - 14%;
- roughness - relevant in the manufacture of external waterproofing masonry.
An ordinary stone is cheaper than a facing one; to reduce the construction budget, it is better to choose this particular option. The size of the red brick affects solely the pace of construction of the foundation masonry. Therefore, the format is not important.
Outside adhesive is a strong, premixed adhesive that is sold in pipes with a nozzle for dispensing small amounts of product. The adhesive is resistant to weathering but not suitable for immersion in water or direct sunlight. Outdoor adhesive is ideal for repairing broken bricks or attaching decorative accessories to bricks.
Epoxy resin is a strong adhesive used to bond stone, wood and metal objects. The putty can enter cracks and crevices and harden to form a strong bond between two objects. Epoxy resin is resistant to water and heat.
When choosing a concrete block, the construction time of the foundation is reduced due to the large dimensions in comparison with even a double stone. The disadvantages of brick foundation technology are:
- the spatial rigidity of the prefabricated structure is by default lower than that of the monolith;
- when waterproofing the outer edges of the tape, pillars, it is very difficult to ensure the tightness of numerous mortar joints.
Hot glue can stick to bricks for temporary uses such as hanging Christmas light fixtures for brick walls... From an environmental point of view, its cultivation is very beneficial for Agriculture and environment and does not need pesticides or herbicides. The stalk is proteinaceous, therefore, separately from the seeds, it is not necessary to apply protective substances for storage or use in construction. This could provide comprehensive solutions for humanitarian projects.
Hemp surprises with its unique versatility in flora... There are about a thousand derived plants: medicines, Automotive industry, Industrial Design, paper, textiles, cosmetics, food, not forgetting about the various building materials who represent greatest interest on this page.
Therefore, prefabricated columnar, strip foundations are often shallow or shallow. This is possible only on rocky, sandy or gravelly soils.
For plinth
With normal horizontal waterproofing of the foundation 2 - 3 layers roll material the bearing part of the basement can be made of porous bricks. Any materials are allowed in the facing layer, for example: silicate, hyper-pressed bricks, crevice, hollow ceramics.
The last decades in Europe, improvement and transformation
Background of the current hemp design
He was looking for a lighter and more insulating alternative to previous materials and made mortar filled with hemp between the old half-timbered structure. Initially it was a matter of hemp straw mineralized, but eventually it was shown that mineralization is not necessary for use in mortars or as a free-flowing filler.It should be noted that most of the hemp stem is made up of hemp, which in turn is the most economical part of the plant and was burned in the fields before discovering various uses. The design was the perfect outlet for the large volume of this material. So far, hemp mortar designs, especially new ones, are mainly based on the inherent structures of hemp wood and mortar, very insulating and without structural functions, compacted in between or outside of it, while the most expensive investment is hidden.
When deciding which brick is better to use, it is necessary to take into account:
- the basement is an independent supporting structure;
- distributes uneven loads from solid walls.
Therefore, it is still better to use solid concrete wall blocks or a solid ceramic stone. Commonly used standard sizes NF or one and a half, double brick to increase the performance of the masonry.
Especially in countries like France and England, a light solution of lime and hemp is applied on walls, between plants, under cover, and sometimes in the hearth. In Germany, he is most valued in rebuilding half-timbered houses survivors of past centuries, solving the current thermal requirements without affecting the structure or aesthetic appearance of the building. Loose hemp granules are also very often used as insulating material for filling between plants or under a lid. By overcoming certain technical difficulties, it is also possible to design a hemp insulating mortar ideal for industrial projects.
Protect concrete blocks, brickwork getting wet in the basement is much easier. It is enough to coat the surface with bituminous mastic, decorate the basement with siding.
What to look for when buying
When choosing a brick for the foundation, you must pay attention to the accompanying documentation. The grade of the stone should be higher than M150, frost resistance from F25, geometric dimensions should be in accordance with GOST.
In England materials for wooden structure separately standing house have a cost of about 0 rubles, not counting labor, and compacted material. These structures have the advantage that the roof can be installed early and the mortar can be kept in the weather for most of the drying process, fully adapted to the climate in humid countries and with forest resources... At the same time, the presence of the structure allows the use of very light mortars, adapted to the thermal effects in these countries.
Building with hemp in Spain
In Spain and others warm countries we have a different situation that prompted me to add other systems of our own and pioneers around the world, such as hemp materials developed for load-bearing structures: cannabis and cannabis. These materials not only provide a more economical design than the hemp-lime structure model, but are even more environmentally friendly as less binder or less energy convertible material is required. These systems have great insulating capacity as well as high thermal inertia and give excellent results in climates where extreme temperatures alternate, walls or radiant floors; and in the restoration of old buildings.
During transportation, unloading and storage, edges often break off, which is not a significant defect. In most cases, plaster waterproofing is used for brick foundations. Irregularities will only increase the adhesion of the protective layer.
When tapping on a ceramic metal object, the brick should have a distinct ringing sound rather than a stifled deaf. The ringing indicates the quality of the raw materials used, the correctness of the firing technology, the absence of microcracks and voids.
Advantages of the hemp design
They form the ideal base for noble finishes such as various plasters. The outstanding properties of hemp are mainly its thermal, acoustic and bioclimatic characteristics, which lead to great energy savings. The protective effect of materials from electromagnetic radiation... The environmental benefits are such that it is used in construction.
The exterior of the brick is an elegant finish, very typical of nation building. But nice results not always achieved; sometimes the stripes separate or the tiles allow moisture to enter due to cracks or failures in sealing, or by absorption of the material itself.
Styling nuances
To increase the reliability of a brick foundation, several conditions must be met:
- whole brick - the masonry must be carefully tied up by displacing the vertical seams in adjacent rows, therefore, it is necessary to select a whole brick, transport it carefully, store it in a building spot, move it at the facility;
- reinforcement - in each 4th row, the dressing of spoons / poke is required, the use of a masonry wire mesh with a cell of 2 x 2 - 5 x 5 cm;
- wetting - it is recommended to lower the brick into a bucket of water at the time of laying it on the bed from the solution;
- additives to the solution - the penetrating mixture will ensure the moisture resistance of the seams;
- foundation - unlike monolithic structures, brick masonry is sensitive to unevenness of the base, the underlying layer of non-metallic materials, it is recommended to pour 5 cm of the screed twice as wide more size strip or columnar foundation.
It is generally believed that cladding bricks are made from solid products using tiles or sheets. These walls of traditional objects have high cost thanks to their skill and specialization. To this must be added more long time execution and use more materials together with organic materials with high environmental impact. In addition, the costs for these departments increase together, taken together, which is the mortar filling the bricks.
These shortcomings will no longer be the same, because the market has appeared New Product which gives the walls appearance traditional brick. The product is complemented by three accessories made in the same ceramic material: lintel or sardinet, corner piece and frieze.
Advice! The brick breaks easily in any direction, so you don't need to buy ¾, halves, ¼, which are more expensive. It is wiser to use an ordinary, and not a face stone, which is not visible underground.
Thus, brick foundation cannot compete with monolithic reinforced concrete structures in terms of service life and spatial rigidity. However, this option will save budget and construction time. He does not need to gain strength for 28 days, the walls can be erected in a week.
Advice! If you need contractors, there is a very convenient service for their selection. Just submit in the form below detailed description works that need to be completed and offers with prices from construction crews and firms. You can see reviews of each of them and photos with examples of work. It is FREE and non-binding.
Sand-lime and ceramic bricks are long-standing competitors in the construction industry. Both of them have a special set of properties and qualities that can make the future construction practical and durable.
Every year, it becomes more and more difficult to make a choice: manufacturers are modernizing technologies and equipment, improving the characteristics of products in order to distinguish them from the rest. In this article, we will try to find out after all: which is better - silicate or ceramic bricks?
Overview of the main characteristics of materials
It is worth starting with a consideration of the basic qualities of the material, because they are usually the decisive arguments in favor of certain products. So, which brick is better: silicate or ceramic? We understand the properties.
Composition and properties of silicate bricks
Sand-lime brick is made from a mixture of lime, water and sand. Moreover, the latter in its composition - most of all in percentage... Also, the composition may contain ash, slag and other components similar in properties and purpose.
The characteristics of future products are in direct proportion to the composition and proportions of the mixture of materials, their indicators can either decrease or increase. Let's look at the average indicators of the qualities of silicate bricks using the table.
Table 1. Technical, physical and operational properties of silicate products:
Index | Its meaning and description |
Thermal conductivity | The thermal conductivity of the products is about 0.7. It is difficult to call silicate brick a leader in this respect. However, if we compare this indicator with the density of products, then it is quite good. |
Frost resistance | Manufacturers assure that these products can withstand up to 100 freeze and thaw cycles. GOST dictates only the minimum value for facial products, which is 25 cycles. |
Shrinkage | We can say that sand-lime brick is quite resistant to shrinkage. |
Water absorption | The percentage of moisture absorption is from 6 to 16%. If we compare silicate brick with aerated concrete, then the indicator is quite competitive. However, the products still need protection from moisture. |
Strength and density | The density of the products is high. Also, the material boasts high bending and compressive strengths. |
Environmental friendliness | The composition of silicate brick does not contain harmful and hazardous substances, therefore it is environmentally friendly. |
Fire resistance | In accordance with GOST, the material does not burn. |
Vapor permeability | Silicate brick helps to establish a favorable microclimate by means of steam exchange. The indicator is 0.11. |
Soundproofing | The ability to sound insulation is, however, silicate brick cannot be called a leader in this regard. |
Cost of materials | The price of products depends on many factors: the region, the type of brick, and sometimes the number of voids. However, in general, we can say that the price category is average. |
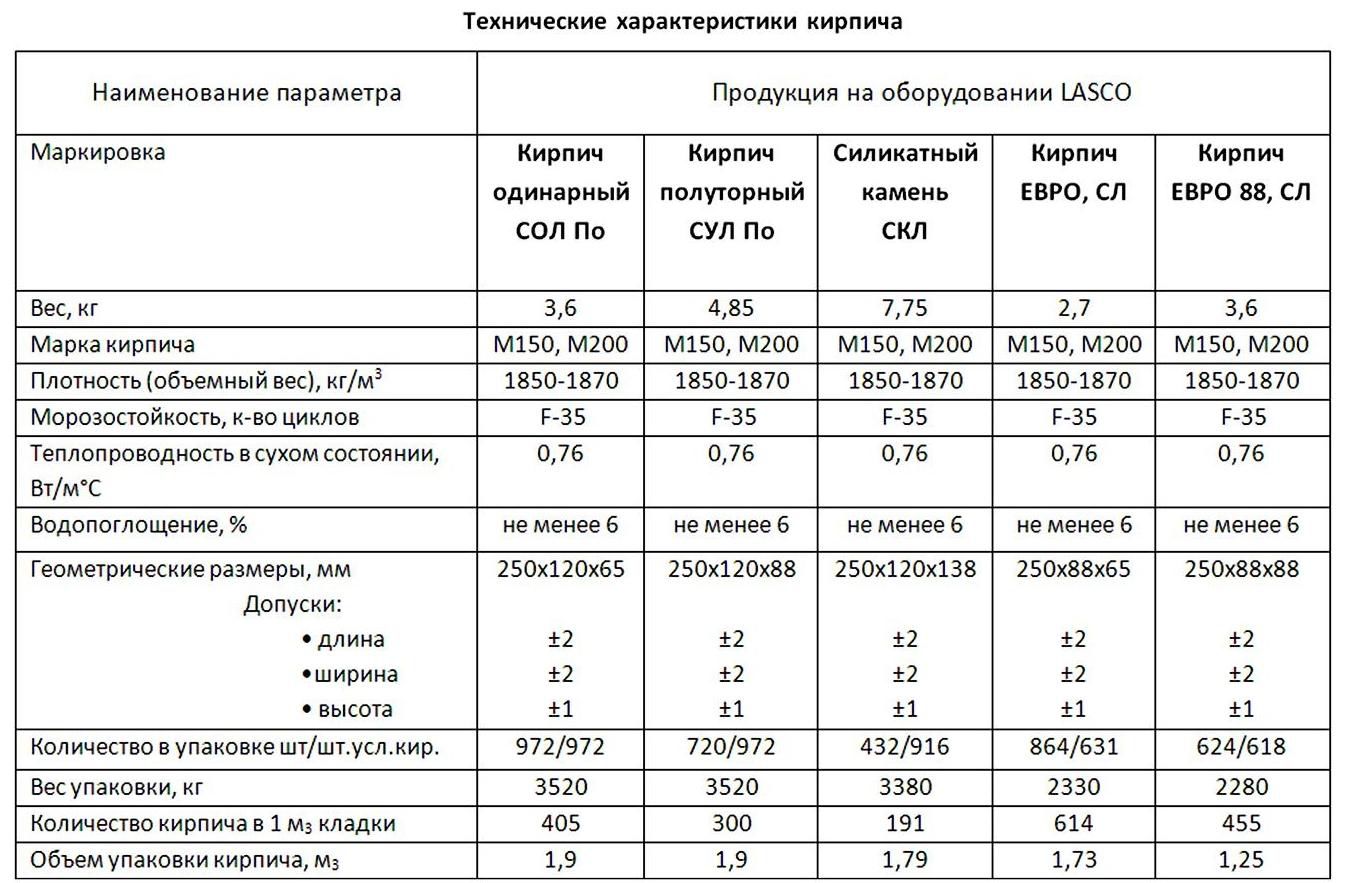
The main indicators of the qualities of ceramic bricks
Ceramic brick has not lost its popularity for decades, and it is well deserved. Let's make sure of this and consider a table that reflects the main characteristics of the material.
Table 2. Characteristics of ceramic bricks:
The above indicators are indicative, since the exact values depend directly on the type of products, which can be characterized by different numerical values of properties. Now we will consider them.
Product classification
In order to understand which is better: sand-lime brick or ceramic, it is worthwhile to thoroughly consider the possible range of products and the specifics of the use of materials. We will start with silicate products.
Types of silicate bricks and their scope
Depending on the size, sand-lime brick is:
- Single;
- One and a half;
- Double.
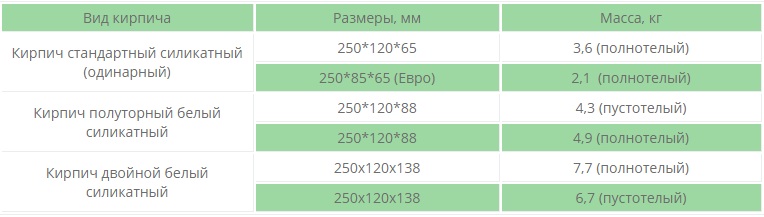
Single has a size of 250 * 120 * 65, one and a half has a height of 88 mm, and a double has a height of 138 mm. Structurally, products can be solid and hollow.
Solid bricks are stronger, denser and heavier:
- It has a high thermal conductivity coefficient.
- It can withstand significant loads.
- It is used for the construction of walls, partitions and other structures of buildings and structures.
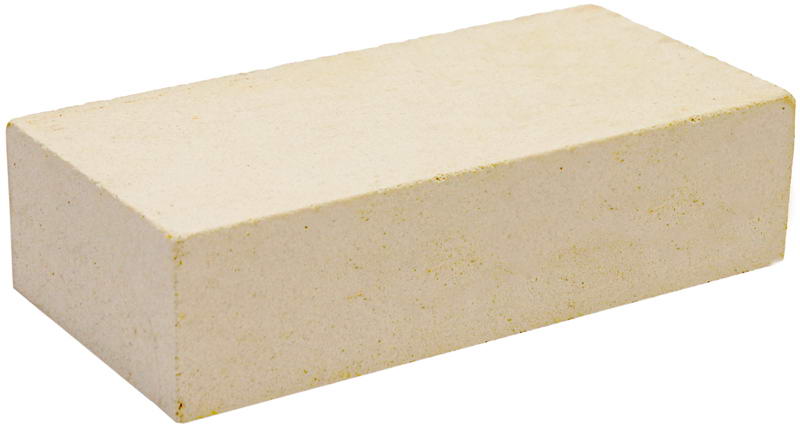
Hollow - on the contrary: it is lighter in weight, less durable, its ability to retain heat is increased.
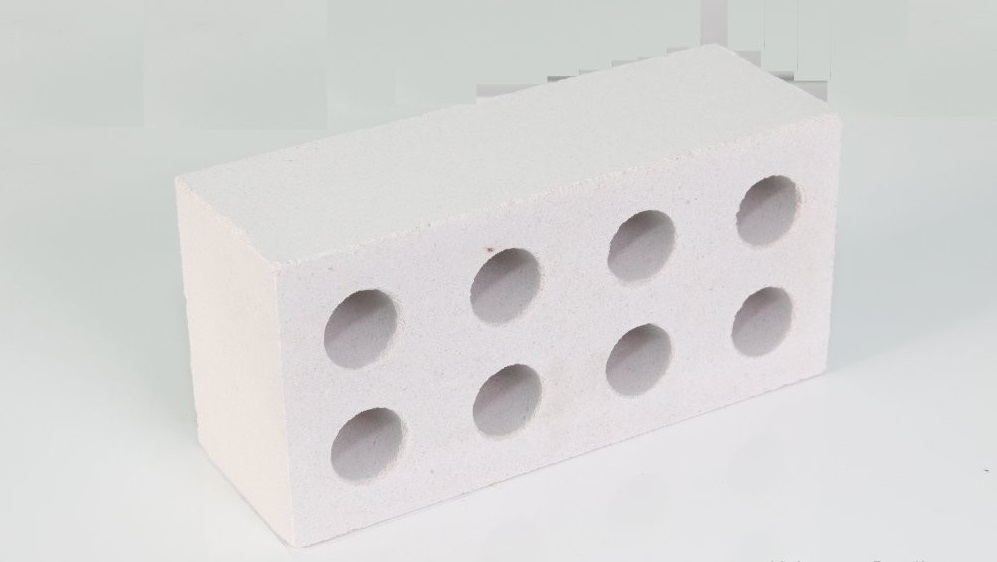
Such products may have voids. of various shapes and in different quantities. Standard options are as follows:
- 3 hollow bricks;
- 11 hollow bricks;
- 14 hollow bricks.
The first option is characterized by a voidness of 28-30%, the second - 20-25%, and the third - about 15%.
Note! GOST dictated the requirement for the nature of the voidness of the products: they should not be through.
Also, the technical documentation allows the manufacture of products with other voids as agreed with the consumer. Depending on the purpose, sand-lime brick can be: ordinary and front.
Ordinary products are used for the main masonry, they need subsequent finishing. The requirements for them are not so high. Their surface may have roughness, and the corners may have small chips.
Facial, or facing brick must have high external characteristics. Their surface can be smooth or textured.
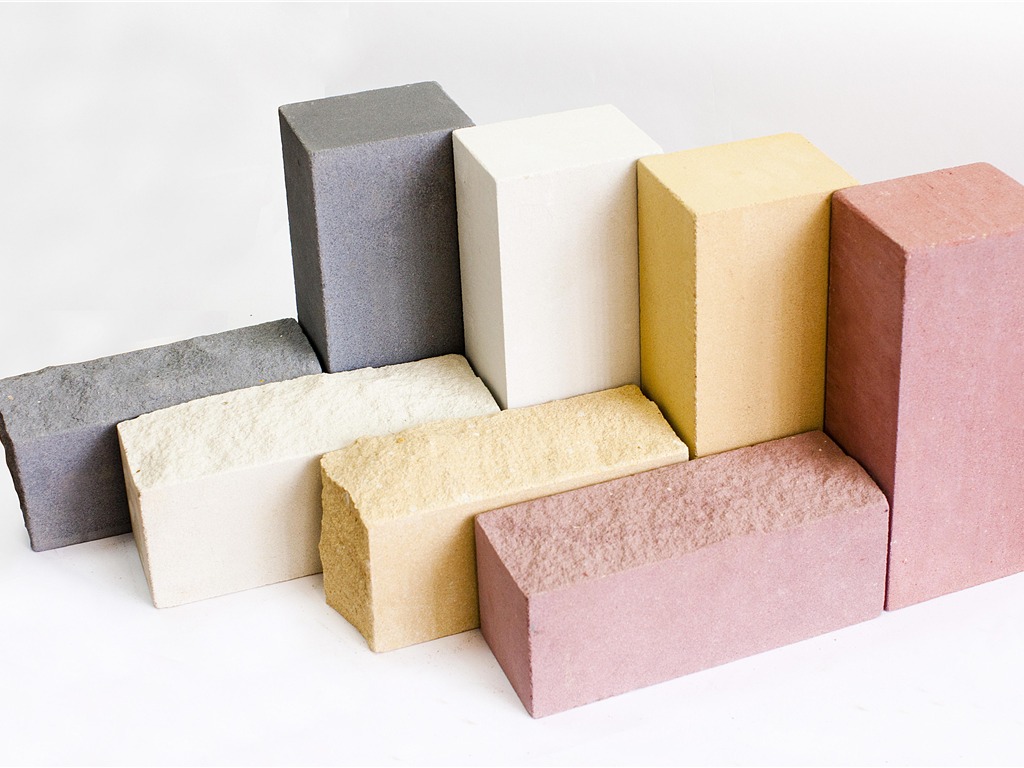
According to GOST, there should be two decorative sides - a spoon and a butt side, however, again, by agreement with the consumer, it is allowed to produce products with one decorative side. If we talk about color solution products, then you can distinguish painted and unpainted brick. The latter is white or slightly grayish in color.
Tinted products can have almost any shade. The content and proportions of components in the manufacture of sand-lime bricks can be slightly adjusted.
Depending on the availability of certain components, products can be:
- Lime-sand, containing lime and sand;
- Lime-ash, characterized by ash and lime content;
- Lime-slag containing lime and slag.
If we talk about the scope of the material, then it is wide enough:
- During the construction of buildings and structures;
- When building ventilation ducts;
- When building fences, partitions and other structures.
Varieties of ceramic bricks and their use in construction
Ceramic brick has a fairly extensive classification. Each of them is based on a specific characteristic. Consider, using the table, what product options brick manufacturers can offer.
Table 3. Classifications of ceramic bricks:
Basis of classification | Types of ceramic bricks | Description and comments |
Depending on the purpose of the products, ceramic bricks can be | Ordinary | It is used in the construction of walls and partitions, maybe, in turn, hollow and full-bodied. |
Facing | Such a brick is distinguished by increased external characteristics. Products do not need subsequent finishing and serve as cladding material. Manufacturers offer different colors and shades of products. |
|
According to the structure of the brick, products are | Hollow | They differ in the presence of voids, the shape and number of which may be different. Such products are lighter in weight and less durable. They are used for the construction of partitions and for facing structures. |
Corpulent | The most heavyweight and dense products... They can withstand significant loads. With its help, load-bearing walls and partitions are erected. |
|
The variability of product sizes also provided the basis for the emergence of classification. In accordance with it, a brick can be: | Single | Has a size of 250 * -120 * 65, marked - 1NF. |
One and a half | Have a size: 250 * 88 * 120. Marked - 1.4 NF. | |
Double | Product size: 250 * 138 * 120. Marking - 2.1 NF. | |
Euro | Its size: 250 * 65 * 85. | |
Ceramic bricks are also classified according to the strength grade. | M50 | Such products are the least durable of all. They are used in the construction of structures and their elements, which will not be subject to significant loads. This can be, for example, fence posts. |
M100 | Such bricks are used in the construction of walls and partitions for any purpose, provided that they are not load-bearing. | |
M125 | This grade of strength is quite enough for the construction load-bearing walls. | |
М150, 175, 200 | The most durable products. They are used in the construction of load-bearing walls and even a basement. |
Facing ceramic brick
It is worth noting that ceramic bricks have profile products in their assortment, which significantly expand the architectural possibilities in the construction of buildings.
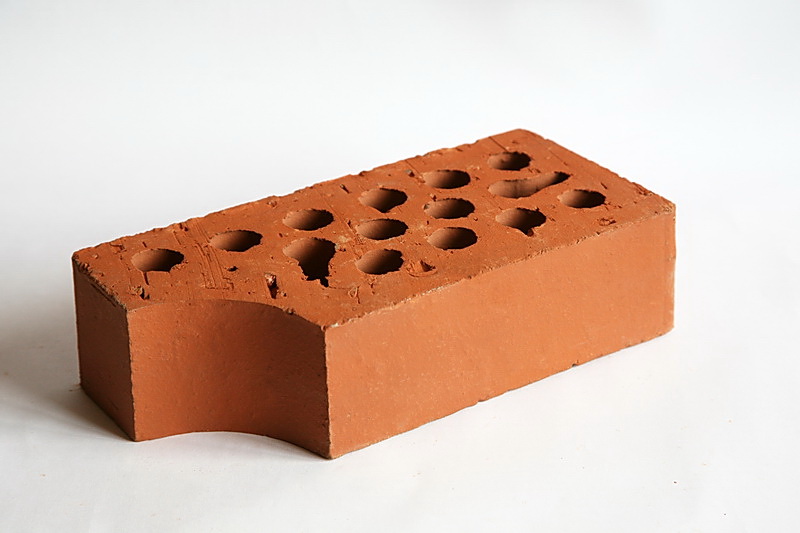
And now it will be appropriate to compare the indicators of the quality of products different types... Let's use the table.
Table 4. Characteristics of different types of ceramic bricks:
Brick type | Frost resistance | Thermal conductivity | Density | Compressive strength | Porosity |
Facing | 35-75 | 0,25-0,26 | 1300-1400 | 75-250 | 6-14 |
Hollow | 15-50 | 0,3-0,5 | 1000-1450 | 75-150 | 6-8 |
Super efficient | 15-50 | 0,24-0,26 | 1100-1150 | 75-300 | 6-10 |
Corpulent | 15-50 | 0,6-0,7 | 1600-1900 | 75-300 | 8 |
Clinker | 50-100 | 1,16 | 1900-2100 | 450-1000 | 5 |
Strengths and weaknesses of both materials
Since we have already examined the indicators, let's analyze what advantages and disadvantages both materials have and find out: which is better - silicate or ceramic bricks? Which of the products are most vulnerable?
Pros and cons of silicate products
Silicate brick has a number of positive characteristics... The pluses include:
- A sufficiently high index of frost resistance indicates the practicality and high performance of the material;
- Indicators of density and strength allow to erect not only small, but also multi-storey buildings using these products;
- The wide scope of application of the material indicates its partial versatility;
- The composition determines environmental friendliness and, accordingly, safety for the environment;
- Fire resistance is a definite plus, products can also withstand elevated temperatures, which is also important;
- The ratio of density and coefficient of thermal conductivity is quite acceptable;
- Low price;
- The ability to do the masonry with your own hands. In this case, you will need instructions and a minimum set of materials and tools;
- The sound insulation indicator will be able to make the stay in the room comfortable, protecting those in it from extraneous noise;
- A variety of manufacturers, types and shades of products allow each developer to choose the right option for themselves;
- It is also worth noting the high aesthetic qualities and good geometry of the brick.
The main disadvantages are as follows:
- Hygroscopicity of bricks. Products absorb moisture quite intensively, therefore they need additional protection from its impact, since the consequences can be very unpleasant;
- Large weight of products. If we compare silicate bricks, for example, with masonry made of foam or aerated blocks, then the load on the foundation, when constructing a building using silicate bricks, will be much higher;
- Reduced construction speed due to small size products;
- Absence decorative elements in the range of products;
- Silicate bricks are not recommended for use in the construction of objects that are characterized by constant high humidity... For example: a bathhouse or a sauna, as well as the foundations of buildings.
Advantages and disadvantages of ceramic products
Ceramic brick has the following positive characteristics:
- First of all, it is worth noting the durability of the products and the high performance characteristics... In many ways, these qualities have determined the particular popularity of the material, which only grows over the years due to the constant improvement of technology and equipment for production.
- A variety of choices. The market provides an opportunity to purchase products different types and driving. This applies to shape, size, structure and color.
- As with silicate brick, if we compare the thermal conductivity coefficient with the density index, then given fact is undoubtedly a plus.