In construction, an important role is played by the right material. Brick is considered one of best solutions, but it can be different. So what is better - silicate brick or ceramic brick?
Brick has long been considered one of the best materials for building a house. But if in the old days they used only ceramic brickobtained by firing clay, then now it competes with silicone "brother". Of course, it is impossible to unequivocally say which brick is better - silicate or ceramic. But cited in this article detailed description These two building materials will allow you to correlate all the pros and cons. And, therefore, to find the answer to the question: what to choose - silicate or ceramic brick.
Ceramic brick
Ceramic brick
As already mentioned, clay serves as the basis for ceramic bricks.
The main advantages of this material are as follows:
- Excellent frost resistance. Depending on how many freezing and thawing the brick can carry without any damage, the following classes of material are distinguished: F15, F25, F35, F50, F100, etc. Given that winters in Russia are quite different low temperaturesIt’s best to start with at least F35.
- Strength. There is also no single bar for this part: the ability to withstand a certain weight per 1 cm² of load is determined by the characteristics of the M50-M250. If you plan to build a small structure (a small one-story house or a bathhouse), then the M50 will be quite enough. But the larger the building, the stronger the material needed.
- High performance in terms of thermal insulation.
- Fairly high fire resistance. It is for this reason that red brick is used for the manufacture of furnaces, barbecues, etc.
- Environmental friendliness, and, therefore, safety for health.
- Excellent soundproof properties.
However, there are ceramic bricks and cons. The most basic, this is perhaps the price - ceramic brick is one of the most expensive materials for construction, it is also necessary to use only high-quality bonding mortar (to avoid the appearance of efflorescences).
Silicate brick
Silicate Brick
Silicate bricks as an alternative to ceramic appeared relatively recently - something about a century ago. The main difference between silicate brick and ceramic brick is that the raw material for it is not clay, but sand and lime, which are processed by autoclaving. If we compare the silicate and ceramic bricks, then in terms of frost resistance and strength the brick made of lime is not inferior to clay, and in sound insulation it is significantly superior. The price of these two materials is also significantly different.
But all according to some characteristics, silicate brick is significantly behind its clay counterpart:
- Excessive moisture absorption. Lime and sand absorb moisture too much, therefore it is not recommended to use silicate brick for building a house in an area with too high humidity.
- Average refractoriness. If we talk about building materials in general, the performance of silicate brick cannot be called bad, but it certainly loses to red brick. Therefore, for the construction of stoves, fireplaces and other things like that white brick not good.
- Low thermal conductivity. To some extent, it depends on the density of the material, but it can still be said quite confidently that this building material keeps heat very mediocre.
Due to the above qualities of silicate brick, it is used mainly for the construction of internal partitions - good sound insulation will provide comfort to people living in the house, and thermal insulation in this case will not be too important.
What material is more suitable for construction
Talking about what kind of brick will become the best material - silicate or ceramic, you need to take into account all the nuances: the climate at the construction site, the size of the house and much more. In addition, few people will build a house from one material from the base to the roof, because every kind of brick has strengthsthat can be applied in a particular area. So the red brick will become ideal option for bearing walls, as well as those elements that come in contact with open fire. From white, silicate brick, you get good internal partitions. In addition, the brick differs not only in the components from which it was prepared, but also in size, color, fullness (distinguish between solid and hollow bricks) and many other parameters. For example, a brick for wall cladding will significantly differ in characteristics from ordinary, etc. Therefore, it would be more reasonable to select a separate type of brick for a specific task.
10.11.2014
Building stone, called brick, is conditionally divided into two types: clay and silicate. By appearance they differ in color. Clay brick is reddish and silicate brick is off-white. The first is divided into three groups (ordinary, facial, special), each of which has different properties and is intended for different types works. As a rule, silicate brick is used for the construction of aboveground structures and cladding of buildings. This is due to the fact that it has a low density and, accordingly, is less durable. Such a brick is unsuitable for the construction of the foundation.
What material can be used for laying the foundation
The foundation can be built only from one material - solid ordinary brick. Facing is suitable only for facing work. With the help of a special brick, the laying of stoves, fireplaces and chimneys is performed, since it is refractory.
The main advantages of red ceramic bricks are high moisture resistance, strength, and thermal conductivity is within normal limits. Today this buy a brick possible in almost any hardware store or on a site, such as agroprombud.com.ua. It can be used for erection. underground structures. However, do not forget about moisture protection. Although, over short term water is not able to destroy the material, it will gradually be absorbed inward. Prevent her negative influence only high-quality waterproofing is capable. You can perform it using bitumen mixtures, roofing felt and special mastics with water-repellent properties.
Proper selection of materials is the key to the durability of the building. AND front brick should also give it an aesthetic look. The first thing when buying a brick is to pay attention to its appearance, that is, its shape and color. The presence of concave or convex faces indicates violations of technology in the manufacture. For example, such deformations could occur due to excessive firing. Such material is not worth buying. Most likely, it will quickly crack under the influence of moisture and the large weight of the above-ground structure.
Too bright scarlet material is also considered unsuitable for the construction of the foundation. In this case, the firing was most likely insufficient. Quality brick It has a flat and smooth surface of a dark orange hue. The base of such building materials will actually be very durable and will last for a long period of operation.
By brick today it is customary to understand such material that has found application in the construction process and is used to solve the problems of erecting a variety of buildings, not only housing, but ...
Increasingly popular are houses built of gas silicate blocks. The silicate block has a porous structure. Houses made of such blocks are warm. The walls erected from this type of blocks have a good ...
Arbolit is a durable and environmentally friendly material that is used in the construction of buildings, like a sandwich panel. The thermal conductivity of arbolite is two times better than that of expanded clay concrete and four ...
Types and characteristics of bricks.
Brick
Types of bricks
The domestic construction market today is ready to offer an abundance of a variety of wall materials. But, at the same time, the traditional building brick does not lose its relevance, although it can be considered one of the oldest building materials. Naturally, today's types of bricks are very different from their ancestors. So, they perfectly retain heat, tolerate high humidity and any temperature conditions and, therefore, are ideally suited for the construction of buildings in Russia. The philistine point of view divides the brick into red and white. However, there is a wide variety of types of bricks. This diversity is explained by the respective fields of application. Bricks vary not only in size and shape, but also in composition, production technology. Brick is one of the most popular building materials, but it can be difficult to figure out its variety.
Brick: workmanship
- The brick is ceramic.
This view bricks are made of clay, less often a mixture of varieties of clay. After molding and drying, such a brick undergoes high-temperature firing in a furnace heated to 1000 degrees Celsius. Ceramic brick that has not spent enough time in the furnace differs in color (it is lighter than usual), as well as in a dull sound. High-quality brick has a matte surface, and upon impact it emits sonorous sound. At a break, such a brick has a porous structure, it is light in weight and homogeneous in appearance. If the brick has cracks on the outside, as well as voids inside, it is considered that it is defective. Basic requirements for finished products must comply with GOST 530-2007 "Brick and ceramic stones."
- Silicate brick.
This type of brick is made of sand and lime. The main advantages of silicate brick are good sound insulation and low thermal conductivity. Even thin walls built of silicate brick will have the same sound insulation and thermal conductivity as much thicker ceramic brick walls. But there are also disadvantages - less moisture resistance, compared with the ceramic version. Therefore, white brick is mainly used for the construction of walls and partitions, and is not used for the construction of fireplaces, stoves, foundations.
- Hyperpressed brick.
Hyperpressed brick is made from special mixturewhere 90% is limestone and another 8% is cement. The remaining two percent of the mixture is represented by special dyes. The mixture is pressed in special forms, after which the bars are obtained perfect shape and colors used for all kinds of facing and finishing work. On the market you can also find hyper-pressed brick with a heterogeneous structure, which is used for cladding under the "fragmentary stone".
Differences in brick by purpose:
- Ordinary brick.
Ordinary or standard brick is widely used for the construction of foundations, as well as construction bearing structures. This brick can be painted or plastered. In this regard, the brick does not need to be endowed with high aesthetic external qualities. Because of this, a bar of such a brick has a heterogeneous structure and color, it may have various defects, etc., but this does not matter much, since it does not affect the strength of such a brick.
- Facing brick.
This type of brick is also called front, decoration, facade. It can be described as an excellent building material that does not have extraneous defects. In the manufacture of facing bricks, it is important to strictly comply with all prescription and technological standards of manufacture, otherwise, there may be extraneous inclusions, or violations in the structure of the limestone layer. For brick with limestone, moisture is a dangerous factor, as it can provoke chemical reactioncapable of violating the integrity of building materials. In accordance with GOST, presented to all the qualities of a brick, including its appearance, the deviations in size of a facing brick cannot exceed 4 mm in length, 3 mm in width, and also a couple of millimeters in thickness. Facing bricks, in contrast to the rough one, meet the standards much better. Specialists note two types of front bricks: a textured brick with a relief surface, and shaped brick used to decorate the window openings of cornices and other decorative parts of the building. The non-standard structure and form allows you to create a truly original design any building, giving roundness to the edges.
Fig. 1. Popular colors of front brick.
Ivory, Straw, Red, Terracotta, Brown
- Chamotte brick.
This type of brick is used to perform both internal and exterior decoration fireplaces and stoves. In view of the fact that it must meet the highest operational requirements, such a brick has heavy weight, good density, resistance to strong heating, manifested in the ability to withstand temperatures of the order of 1000 degrees. Often, refractory brick has a yellow (sand) tint.
- Clinker brick.
The name of clinker brick is closely related to the technology of its production. During this procedure, the clay layers are sintered to form a solid mass. As a result of this procedure, it is possible to avoid the appearance of many defects, such as structural defects and extraneous inclusions. Since clinker brick is homogeneous, it can be considered one of the strongest building materials. In addition, it is not limited in texture and colors, which allows it to cover numerous needs. domestic market, because it can be used to perform a wide range of works, such as paving, cladding, etc.
Separation of ceramic bricks by the manufacturing method:
Plastic Molding Bricks
This brick is very popular because it has no restrictions on use. It is made by pressing the initial mass under high pressure. The resulting bar is dried and fired. In a special furnace, the brick is heated to a temperature of 800-1000-chu degrees. Sometimes, the temperature can exceed the barrier of 1000 degrees, if construction requires it.
Semi-Dry Bricks
Semi-dry brick is made of clay by pressing and firing. For these purposes, there is no need to dry the brick. But, the scope of this brick is quite limited, since it has a porous structure and, therefore, becomes vulnerable to high humidity. As a result, it cannot be used for the construction of load-bearing walls, fences or structures, since they will not be durable. This brick has been successfully used for the construction of internal ceilings and walls, due to its smooth surface and perfect geometry. Semi-dry brick walls do not need to be leveled at all, which saves time and money.
Characteristics of a brick.
The concept of void brick
Ceramic bricks, which are also often called masonry bricks, clay, backing, red, can be hollow and solid.
Solid brick
A solid brick has no voids, having a smooth or corrugated knurled structure for the convenience of applying plaster.
Hollow brick
This brick has through holes (voids) different shapes and size, which makes it rather light. This quality reduces the load on the foundation. At the same time, thanks to high thermal conductivity, even walls of small thickness allow excellent heat storage in the room. The cost of a solid brick is often higher than the cost of a slot analog .
Fig. 2. The voidness of the brick.
Solid and slotted (hollow) brick
Weight and size of the brick.
During construction, three standard brick sizes are used:
Single brick
Also called single-row bricks. The standard size of such a brick: 250x120x65 mm. The weight of a standard brick is 2-2.3 kg. ;
One and a half brick
Such a brick has a size of 250x120x88 mm., Where 88 mm. this is the height. The weight of one unit is 3-3.2 kg. ;
Double brick
Double brick has the designation 2NF. Dimensions: 250x120x138 mm., Where 138 mm. this is the height. The weight of one unit is 4.8-5 kg.
Today you can also meet not standard sizes brick, such as: European, restoration, etc. It should be noted that the size of the brick must be known in advance when calculating the amount of brick required for construction.
Brick grade, strength
Brick strength - his main characteristic, implying the ability of a brick to resist loads, deformations and internal stresswhile maintaining their physical integrity. Strength in the marking is indicated by the letter "M" and a numerical designation. The number in the marking indicates permissible load in kilograms per square centimeter according to GOST 530-2007.
By its strength, brick is divided into such brands:
The most durable will be a brick with a maximum numerical value. The brick brand in accordance with the strength parameters will be determined based on two parameters: ultimate strength at the time of compression and ultimate tensile strength. It should be noted that the flexural strength is approximately 20 percent of the compressive strength. It should be said that the strength of the brick during compression is quite high. For a better understanding, we give an example: a batch of brand 100 bricks. We get the following indicators: the compressive strength is at least one hundred kilograms per square centimeter (or ten MPa), that is, literally every square centimeter of the surface of this brick is able to withstand a load of at least one hundred kg Standard brick bed area building material equals 300 cm². Knowing this, it is quite easy to calculate what kind of load is required in order to destroy it. This figure is 30 thousand kg.! Of course, you need to understand that in masonry, bricks work not only on compression, but also on bending - due to the presence of layers of cement and bricklaying using dressings. So, the bearing masonry ability of a brick is taken below the strength of the brick itself. The brand of strength of brick M100 is popular, it is used in the construction of buildings up to 5 floors - kindergartens, individual houses, cottages, schools, shopping centers etc. Higher grade - M200 is suitable for erection high-rise buildings and facilities. The strength of masonry is approximately 60% dependent on the mortar formulation, for example, with a wall height to thickness ratio of 22 (thickness 1.5 bricks, 8 meter wall), the grade of the mortar cannot be less than M50. The cost of a brick depends on its brand.
Brick frost resistance
Main reason The destruction of brick favors a changeable climate. To determine the resistance of a particular type of brick to various climatic changes, a special characteristic called frost resistance was introduced. So, frost resistance of a brick implies the ability of a material to withstand thawing and freezing cycles in a water-saturated state. Frost resistance is indicated by “mrz” or “F” with a numerical index indicating the number of thawing cycles.
The following frost resistance grades are available:
The higher the number, the more resistant the brick is to frost. The frost resistance of a brick is determined during standard tests, in which the brick is immersed in water for eight hours, and then sent for the same amount of time in freezer. The operation is repeated until the brick begins to change its characteristics: mass, strength, etc. At the end of the experiment, an expert conclusion is made about the frost resistance of the brick. As a rule, this indicator does not fall below 25 - 50, less often - 75 cycles. Brick frost resistance grade is selected in accordance with normative documents. For example, for construction in the Moscow region, it is necessary to use a brick whose frost resistance is not less than 35, and even better than 50 cycles. The frost resistance index of a brick directly depends on its ability to absorb moisture. To determine the water absorption parameter of the brick, a dry bar is taken and immersed in water for 48 hours. Then the brick is weighed, after which it is possible to determine the weight of the water absorbed into the brick. According to the requirements of GOST, the weight difference between wet and dry bricks should be in the range of 12-15 percent for the front option and about 6 percent for the ordinary brick.
Brick thermal conductivity
Brick thermal conductivity call it the ability to conduct thermal energy through its own structure. Thermal conductivity is expressed by the coefficient of thermal conductivity (λ - "lambda"). That is, thermal conductivity is an indicator of how much heat energy (W) is lost by each square meter the outer surface of the brick with a one-meter thickness and the temperature difference between the inner and outer surfaces of one degree. The less energy is lost, the better. Based on this, the smaller the coefficient of thermal conductivity of the brick, the warmer it will be indoors. The thermal conductivity of a brick depends on its density. The lower the density, the lower the thermal conductivity. The strongest and heaviest brick clinker of the M-500 brand has the highest coefficient of thermal conductivity, while the less durable and lightweight ceramics of the M 75 brand, respectively, the lowest level of thermal conductivity. Also, the number of voids affects this indicator. The more voids there are in the brick, the more effective it is in the process of heat preservation.
Black core in brick, contact spots on the surface.
Often you can meet the question, why is the brick black inside? The answer is contained in GOST 530-2007 "Brick and stone ceramic." In particular, paragraph 3.20 of the Technical Conditions describes that a contact spot at a brick is a section of the surface of a brick that differs in color. This section occurs during drying or firing, and does not affect the characteristics of the brick. Paragraph 3.22 defines the black core of a brick as the area inside a brick formed as a result of iron oxide during firing. Clause 5.2.5 suggests that the facing and ordinary bricks may form a black core and a contact spot on the surface.
Recommendations on which brick is better to use in the manufacture of prefabricated tape or from small-format materials are given in SP 15.13330 of 2012. Masonry from red ordinary, facing full-body ceramic bricks from 51 cm wide or concrete blocks 20 x 20 x 40 cm in size is allowed. With an unlimited budget, you can choose a clinker stone with the highest possible moisture resistance. For the basement part of the foundation, the requirements are much lower than for underground structures.
Despite the variety of wall materials used for masonry, only red ceramic bricks and wall concrete blocks are allowed in the foundations. Ceramics for the foundation are classified according to the following criteria:
- dimensions - normal format (NF) 6.5 x 12 x 25 cm, double (2.1 NF) 14 x 12 x 25 cm, one and a half (1.4 NF) 88 x 12 x 25 cm;
- appointment - front, ordinary;
- frost resistance - F25, F35, F50.
Moreover, manufacturers guarantee the specified frost resistance values \u200b\u200bonly for the basement of the foundation masonry. Structures operating underground have a minimum resource (one and a half times less than reinforced concrete). It is forbidden to use brick strip foundations at a high (less than 1 m from the sole) level of groundwater (UGV) or the possibility of its seasonal rise.
Solid ceramic brick is the most optimal choice.
The characteristics of a solid concrete block are different. Concrete strength is twice as high, frost resistance is F15 - F50, the format is much larger. Each block replaces 8 bricks, masonry is faster. The dimensions allow laying without mocking 40 or 60 cm wide. In the first case, you can save the construction budget. The second option is often used for deep tapes, in which the walls of the underground floor are experiencing serious lateral loads.
Attention! There are bricks measuring 6.5 x 8.5 x 25 cm (0.7 NF) manufactured in Europe, single modules (1.3 NF) 6.5 x 13.8 x 28.8 cm, “three-four” 18 cm , “Halves” 12 cm, “quarters” 6 cm.
For underground structures
The main criteria for deciding what is the best brick to use for underground masonry are:
- strength - is standardized only for brands M100 - M300 (2.2 - 4.4 MPa, respectively);
- water absorption - 6 - 14%;
- roughness - relevant in the manufacture of external waterproofing masonry.
Ordinary stone is cheaper than facing, in order to reduce the construction budget it is better to choose this option. The dimensions of red brick exclusively affect the pace of construction of the foundation. Therefore, the format is not fundamental.
When choosing a concrete block, the construction time of the foundation is reduced due to the large size in comparison with even double stone. The disadvantages of brick foundation technology are:
- the spatial rigidity of the prefabricated structure is lower by default than that of a monolith;
- when waterproofing the outer edges of the tape, pillars, it is very difficult to ensure the tightness of numerous mortar joints.
Therefore, prefabricated columnar, strip foundations are often slightly shallow or not deep. This is only possible on rocky, sandy or gravelly soils.
For basement
With normal horizontal waterproofing of the foundation with 2 - 3 layers roll material the bearing part of the base can be laid out of porous brick. Any materials are allowed in the facing layer, for example: silicate, hyper-pressed brick, slit, hollow ceramics.
When deciding what is the best brick to use, consider:
- the base is an independent supporting structure;
- distributes uneven loads from capital walls.
Therefore, it is still better to use solid concrete wall blocks or full-bodied ceramic stone. Usually, standard sizes of NF or one and a half, double bricks are used to increase the masonry productivity.
Protect concrete blocks, brickwork getting wet in the basement is much easier. It is enough to coat the surface with bituminous mastic, decorate the base with siding.
What to look for when buying
When choosing a brick for the foundation, you need to pay attention to the accompanying documentation. The brand of stone should be higher than M150, frost resistance from F25, geometric dimensions correspond to GOST.
During transportation, unloading and warehousing, the edges often break off, which is not a significant defect. In most cases, plaster waterproofing is used for the brick foundation. Roughnesses will only increase the adhesion of the protective layer.
When tapping a ceramic metal object, the brick should have a distinct, loud sound, not a choked deaf. Ringing indicates the quality of the raw materials used, the correctness of the firing technology, the absence of microcracks and voids.
Styling nuances
To increase the reliability of the brick foundation, it is necessary to fulfill several conditions:
- whole brick - the masonry should be carefully bandaged by displacement of vertical seams in adjacent rows, therefore it is necessary to choose a whole brick, carefully transport it, store it in a building spot, move it on the object;
- reinforcement - in each 4 row binding of spoons / poke is mandatory, the use of wire masonry mesh with a cell 2 x 2 - 5 x 5 cm;
- wetting - it is recommended to lower the brick into a bucket of water at the time of laying on the bed from the solution;
- additives in the solution - penetrating mixture will provide moisture resistance of the joints;
- basement - unlike monolithic structures, brickwork is sensitive to unevenness of the base, underlying layer of non-metallic materials, it is recommended to fill in 5 cm of screed twice oversize strip or column foundation.
Advice! Brick easily splits in any direction, so you can not buy ¾, halves, ¼, which are more expensive. It is more reasonable to use an ordinary, not a face stone, which is not visible underground.
Thus, brick foundation cannot compete with monolithic reinforced concrete structures in operational resource and spatial rigidity. However, this option will save the budget and construction time. He does not need to gain strength 28 days, the walls can be built in a week.
Advice! If you need contractors, there is a very convenient service for their selection. Just send in the form below a detailed description of the work that needs to be done and you will receive offers with prices from construction crews and firms. You can see reviews about each of them and photos with examples of work. It is FREE and does not oblige you to anything.
Silicate and ceramic bricks are long-standing competitors in the construction industry. Both of them have a special set of properties and qualities that can make the future construction practical and durable.
Every year, making a choice becomes more and more difficult: manufacturers upgrade technologies and equipment, improving product characteristics, in order to distinguish them from the rest. In this article, we still try to find out: which is better - silicate or ceramic brick?
Overview of the main characteristics of materials
It is worth starting with consideration of the basic qualities of the material, because it is they who are usually the decisive arguments in favor of certain products. So, which brick is better: silicate or ceramic? We understand the properties.
Composition and properties of silicate brick
Silicate brick is made from a mixture of lime, water and sand. Moreover, the latter in its composition - most of all in percentage. Also in the composition may be ash, slag and other components similar in properties and purpose.
The characteristics of future products are directly dependent on the composition and proportions of the mixture of materials, their indicators can both decrease and increase. Let's look at the table using the averaged indicators of the qualities of silicate brick.
Table 1. Technical, physical and operational properties of silicate products:
Index | Its meaning and description |
Thermal conductivity | The thermal conductivity of products is about 0.7. It is difficult to name the leader in this regard silicate brick. However, if we compare this indicator with the density of products, then it is quite good. |
Frost resistance | Manufacturers claim that these products can withstand up to 100 freezing and thawing cycles. GOST dictates only the minimum value for facial products, which is 25 cycles. |
Shrinkage | We can say that silicate brick is quite resistant to shrinkage. |
Water absorption | The percentage of moisture absorption is from 6 to 16%. If we compare silicate brick with cellular concrete, then the indicator is quite competitive. However, products still need protection from moisture. |
Strength and density | Density of products at height. The material also boasts high rates of bending and compression strength. |
Environmental friendliness | Silicate brick does not contain harmful and dangerous substances, therefore it is environmentally friendly. |
Fire resistance | In accordance with GOST, the material does not burn. |
Vapor permeability | Silicate brick helps establish a favorable microclimate through steam exchange. The indicator is 0.11. |
Soundproofing | The ability to soundproofing is, however, silicate brick can not be called a leader in this regard. |
Cost of materials | The price of products depends on many factors: the region, the type of brick, and sometimes the number of voids. However, in general, we can say that the price category is average. |
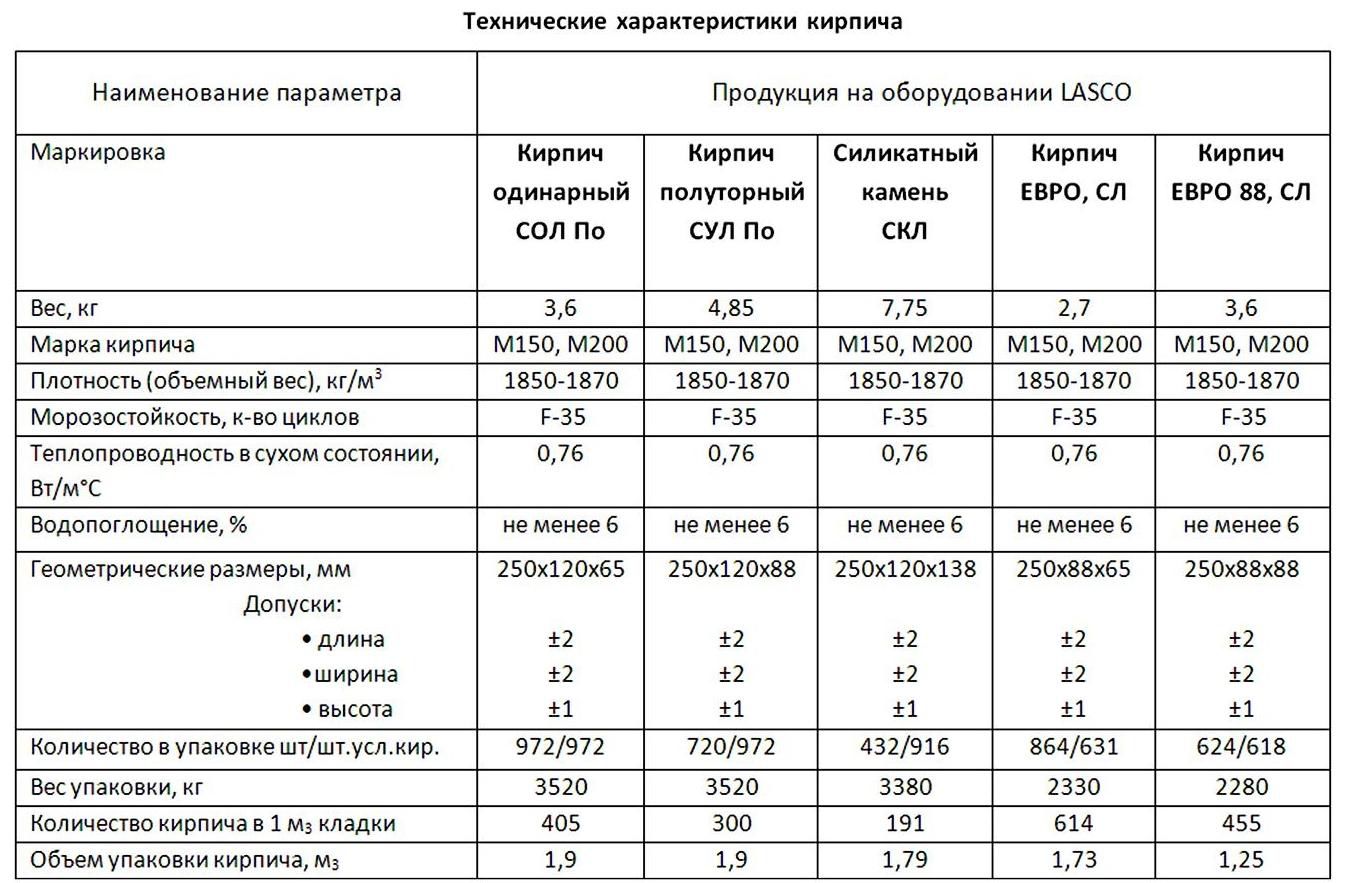
The main indicators of the quality of ceramic bricks
Ceramic brick has not lost its popularity for decades, and it is well deserved. Let's make sure of this and consider a table that reflects the main characteristics of the material.
Table 2. Characteristics of ceramic bricks:
The above indicators are indicative, as the exact values \u200b\u200bdepend directly on the type of product, which can be characterized by different numerical values \u200b\u200bof the properties. Now we will consider them.
Product Classification
In order to understand which is better: silicate brick or ceramic, it is worthwhile to carefully consider the possible range of products and the specifics of the use of materials. We will start with silicate products.
Types of silicate brick and their scope
Depending on the size, silicate brick is:
- Single;
- One and a half;
- Double.
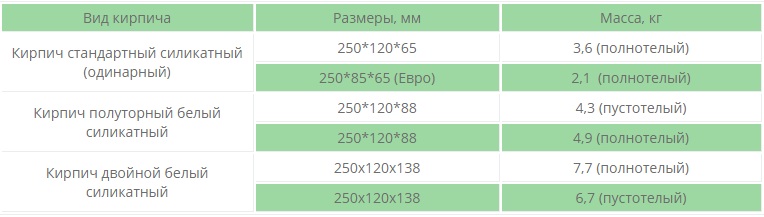
Single has a size of 250 * 120 * 65, one and a half has a height of 88 mm, and double - 138 mm. In a structural respect, the products can be solid and hollow.
Solid brick is more durable, dense and heavy:
- It has a high coefficient of thermal conductivity.
- It can withstand significant loads.
- It is used in the construction of walls, partitions and other structures of buildings and structures.
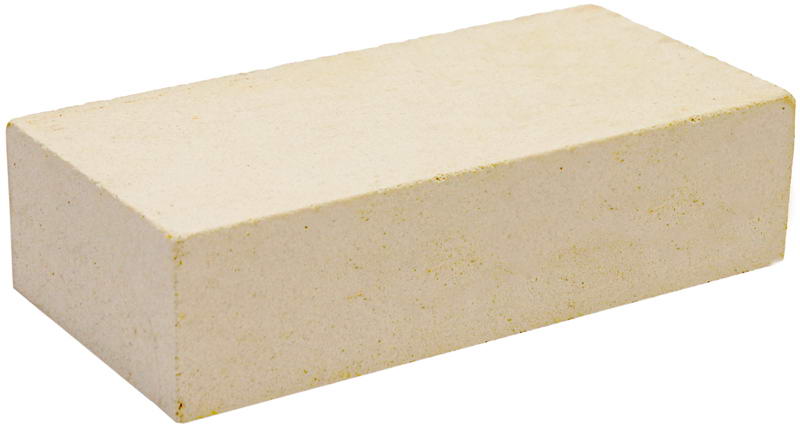
Hollow - on the contrary: more lightweight, less durable, its ability to retain heat - is increased.
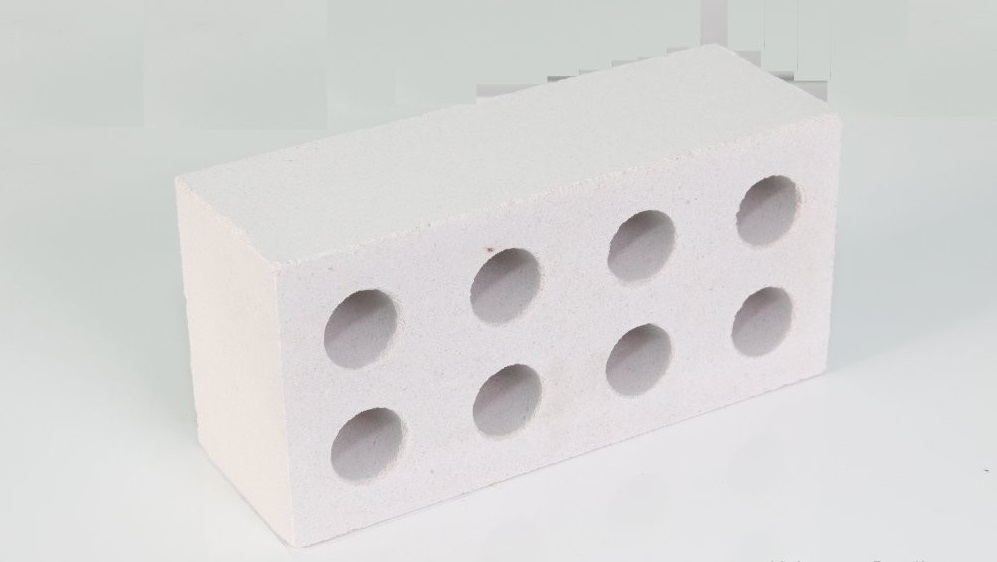
Such products may have voids. various shapes and in different quantities. Standard options are the following:
- 3 hollow bricks;
- 11 hollow bricks;
- 14 hollow bricks.
The first option is characterized by voidness of 28-30%, the second - 20-25%, and the third - about 15%.
Note! GOST dictated the requirement for the nature of the voidness of products: they should not be through.
Also, technical documentation allows the manufacture of products with other voids in agreement with the consumer. Depending on the purpose, silicate brick can be: ordinary and front.
Ordinary products are used in the main masonry, they need subsequent finishing. The requirements for them are not so high. Their surface may have roughness, and the corners - small chips.
Facial, or facing brick must have high external characteristics. Their surface may be smooth or have a texture.
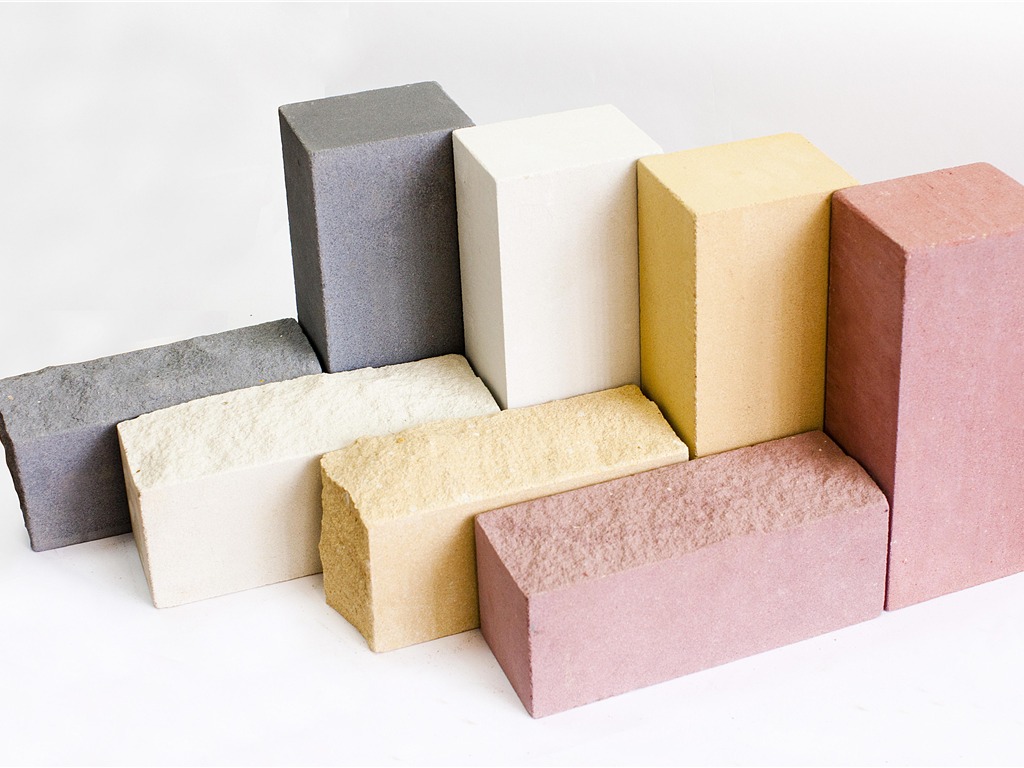
According to GOST, there should be two decorative sides - spoon and bonded, however, again, in agreement with the consumer, the release of products with one decorative side is allowed. If we talk about color scheme products, then you can highlight the brick painted and unpainted. The latter has a white or slightly grayish color.
Tinted products can have almost any shade. The content and proportions of the components in the manufacture of silicate brick can be slightly adjusted.
Depending on the availability of certain components, products can be:
- Lime-sand containing lime and sand;
- Lime-ash, characterized by ash and lime;
- Lime-slag containing lime and slag.
If we talk about the scope of the material, then it is quite wide:
- In the construction of buildings and structures;
- In the construction of ventilation ducts;
- In the construction of fences, partitions and other structures.
Varieties of ceramic bricks and their use in construction
Ceramic brick has a fairly extensive classification. Each of them is based on a specific characteristic. Let us consider with the help of a table what types of products brick manufacturers can offer.
Table 3. Classifications of ceramic bricks:
Classification basis | Types of ceramic bricks | Description and Comments |
Depending on the purpose of the products, ceramic brick may be | Private | It is used in the construction of walls and partitions, which, in turn, can be hollow and solid. |
Facing | Such a brick is characterized by increased external characteristics. Products do not need subsequent finishing and serve as a material for facing. Manufacturers are offered various colors and shades of products. |
|
In accordance with the structure of the brick, the products are | Hollow | They differ in the presence of voids, the shape and quantity of which can be different. Such products are more lightweight and less durable. They are used for the construction of partitions and for cladding structures. |
Corpulent | Most heavy and dense products. Can withstand significant loads. With its help, load-bearing walls and partitions are erected. |
|
Variability in product sizes also provided the basis for the appearance of a classification. According to it, a brick can be: | Single | It has a size of 250 * -120 * 65, marked - 1NF. |
One and a half | Possess size: 250 * 88 * 120. Marked - 1.4 NF. | |
Double | Product Size: 250 * 138 * 120. Marking - 2.1 NF. | |
Euro | Its size: 250 * 65 * 85. | |
Ceramic bricks are also classified according to the strength grade. | M50 | Such products are the least durable of all. They are used in the construction of structures and their elements, which will not be a significant load. It can be, for example, columns for a fence. |
M100 | Such bricks are used in the construction of walls and partitions for any purpose, provided that they are not bearing. | |
M125 | This type of strength is quite enough for the construction of load-bearing walls. | |
M150, 175, 200 | The most durable products. They are used in the construction of load-bearing walls and even a basement. |
Front ceramic brick
It is worth noting that ceramic bricks have profile products in their assortment, which can significantly expand architectural capabilities in the construction of buildings.
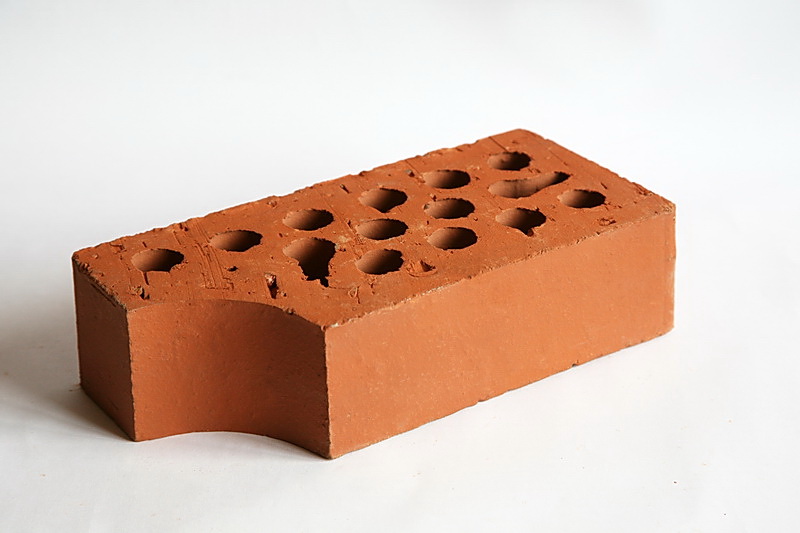
And now it will be appropriate to compare product quality indicators various kinds. We will use the table.
Table 4. Characteristics of various types of ceramic bricks:
Type of brick | Frost resistance | Thermal conductivity | Density | Compressive strength | Porosity |
Facing | 35-75 | 0,25-0,26 | 1300-1400 | 75-250 | 6-14 |
Hollow | 15-50 | 0,3-0,5 | 1000-1450 | 75-150 | 6-8 |
Super efficient | 15-50 | 0,24-0,26 | 1100-1150 | 75-300 | 6-10 |
Corpulent | 15-50 | 0,6-0,7 | 1600-1900 | 75-300 | 8 |
Clinker | 50-100 | 1,16 | 1900-2100 | 450-1000 | 5 |
Strengths and weaknesses of both materials
Since we have already examined the indicators, let's analyze the advantages and disadvantages of both materials and find out: which is better - silicate or ceramic brick? Which of the products are most vulnerable?
Pros and Cons of Silicate Products
Silicate brick has a number of positive characteristics. The pluses include:
- A sufficiently high indicator of frost resistance indicates the practicality and high performance characteristics of the material;
- Density and strength indicators make it possible to erect not only low, but also multi-story buildings using these products;
- The wide scope of the material speaks of its partial universality;
- The composition determines the environmental friendliness and, accordingly, safety for the environment;
- Fire resistance is a definite plus, also products can withstand elevated temperatures, which is also important;
- The ratio of density and thermal conductivity is quite acceptable;
- Low price;
- The ability to make masonry with your own hands. In this case, you will need instructions and a minimum set of material and tools;
- The sound insulation indicator will be able to make the stay in the room comfortable, protecting it from extraneous noise;
- A variety of manufacturers, types and shades of products allow each developer to choose the right option for themselves;
- It is also worth noting the high aesthetic qualities and good geometry of the brick.
The main disadvantages are as follows:
- Hygroscopicity of a brick. Products absorb moisture quite intensively, so they need additional protection from its impact, since the consequences can be very unpleasant;
- Heavy weight products. If you compare silicate brick, for example, with masonry from foam or gas blocks, then the load on the foundation, when building a building using silicate brick, will be significantly higher;
- Reduced construction speed due to small size products;
- Lack of decorative elements in the assortment of products;
- Silicate brick is not recommended for the construction of facilities that are characterized by constant high humidity. For example: a bathhouse or sauna, as well as the foundation of buildings.
Advantages and disadvantages of ceramics
Ceramic brick has the following positive characteristics:
- First of all, it is worth noting the durability of products and high operational characteristics. In many respects, these qualities led to the special popularity of the material, which over the years only grows in connection with the continuous improvement of technology and equipment for production.
- Variety of choices. The market provides an opportunity to purchase products different types and driving. This applies to shape, size, structure and color.
- As with silicate brickif we compare the thermal conductivity coefficient with the density index, then this factcertainly a plus.